Estimated reading time: 5 minutes
As a seasoned masonry contractor, I’ve noticed that people often wonder, “Why does this cost so much?” It’s a valid question—after all, these projects are investments in the strength and beauty of your property. Today, let’s break down these expenses into manageable parts, so you can feel confident in your understanding of what goes into masonry pricing.
Here’s what we’ll cover:
- The main factors that determine pricing for masonry projects.
- A detailed look at labor, materials, and other components.
- Practical tips to get the best value for your budget.
- Common pitfalls to avoid when selecting a contractor.
With that in mind, let’s dive in.
1. What Determines Masonry Costs?
Masonry pricing isn’t arbitrary; it’s shaped by multiple factors that influence the final bill. Here are the most significant ones:
Labor:
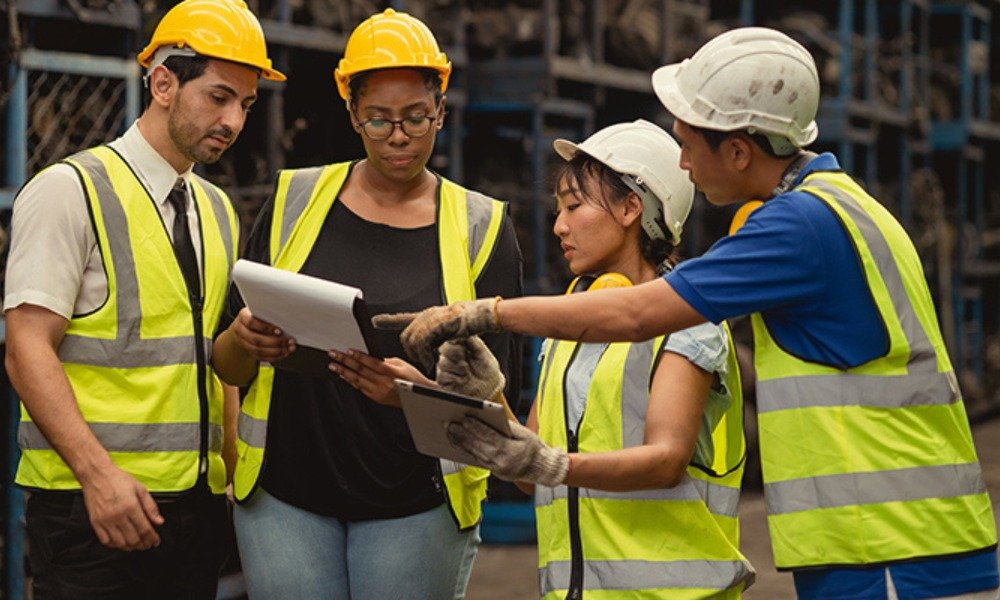
The time and expertise required to complete a project safely and effectively.
Material Selection:
Different options, such as brick, stone, or concrete, vary in price and availability.
Project Complexity:
More intricate designs or larger-scale jobs naturally require more effort and resources.
Location:
Urban areas or regions with higher demand often come with increased expenses.
Each of these elements plays a role in the overall expense, but understanding them can help you better plan and prioritize.
2. The Breakdown of Masonry Costs
Let’s take a closer look at how costs are divided for most projects. This helps clarify why quotes from experienced contractors may seem higher but are worth every penny.
a. Labor
Labor is often the largest portion of a masonry budget. Skilled professionals don’t just stack bricks—they create structures that last decades. These jobs are physically demanding and require careful attention to detail. While rates can vary, investing in trained workers ensures your project is done correctly the first time.
Pro Tip: Don’t sacrifice quality for lower rates. Inexperienced labor may lead to mistakes that cost more to fix later.
b. Materials
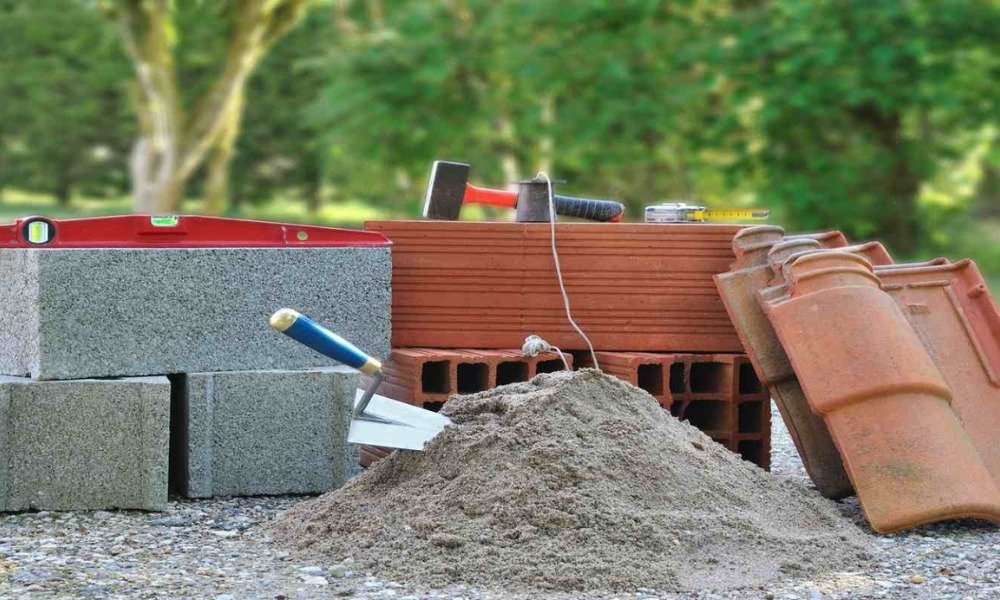
The type and amount of materials directly affect pricing. Bricks, stones, and mortar are essential components, but not all are created equal. Choosing premium options or matching existing styles can increase expenses, while standard materials may save on cost.
Fun Fact: Sourcing the perfect match for a repair job can feel like finding a needle in a haystack. That’s why it’s best to let experienced contractors handle it.
c. Overhead and Administrative Costs
Running a masonry business involves more than just showing up with tools. Overhead includes licensing, insurance, and even estimating services that are often offered for free. These hidden costs ensure the contractor’s operations run smoothly and safely, which is essential for long-term reliability.
d. Equipment and Disposal
Heavy machinery and waste disposal are sometimes necessary for larger projects. Excavators, scaffolding, and dump bins all come with rental fees or maintenance costs. These are factored into your quote to cover every aspect of the job.
3. Avoiding Common Mistakes
Going for the cheapest option may seem like a good idea, but here’s why it’s worth reconsidering:
Skill Gap: Lower quotes often mean less experience. With masonry, precision matters more than cutting corners.
Rushed Jobs: Contractors working for significantly less might skip crucial steps, risking the integrity of your structure.
Hidden Risks: Unlicensed or uninsured providers could leave you liable for accidents or incomplete work.
When comparing estimates, focus on the value of the service rather than just the price tag.
4. Maximizing Your Masonry Budget
Here are some tips to help you get the most out of your investment:
- Bundle Projects: Combining multiple tasks can save money on labor and transportation costs.
- Choose Standard Materials: While premium options are tempting, standard ones often deliver similar results at a fraction of the price.
- Maintain Your Structures: Regular upkeep can prevent costly repairs down the line. For more tips, check out my article on weatherproofing your masonry.
5. An Example Project
Let’s say you need to close an opening in a commercial building. This project involves:
- Labor: A skilled team for two days to ensure proper sealing and alignment.
- Materials: Concrete blocks for the interior and bricks for the exterior, matched to existing designs.
- Overhead: Administrative costs, transportation, and small tools.
After accounting for all these elements, you’ll receive a detailed quote. This transparency helps you understand exactly where your money is going.
6. Final Thoughts
Understanding the expenses behind masonry projects doesn’t just help you plan better—it highlights the skill and effort behind the craft. Quality work is an investment, and while cheaper alternatives might seem appealing, they rarely deliver the durability or beauty that professional craftsmanship ensures.If you’re ready to take the next step, don’t hesitate to reach out or explore related topics like choosing the right contractor for your needs. Together, we can build something that stands the test of time!