Estimated reading time: 6 minutes
Last updated on August 14th, 2025 at 08:58 am
Creating a material take-off (MTO) is an important part of the construction process. An MTO is a document that lists all the materials necessary to complete a specific project and estimates their cost. It also takes into account any labor or equipment costs associated with the project. Knowing how to create an accurate and well-crafted MTO can help you stay on budget, keep projects organized, and ensure success from start to finish.
The first step in creating an MTO is to do some research about the project scope and specifications. Work closely with your client or supervisor to get as much detail about the project as possible – this will make it easier for you when it comes time to estimate costs later on. Once you have determined what needs to be done, it’s time for you to evaluate if certain items need additional resources like tools, equipment, or subcontractors.
What is a Material Take Off?
What is a Material Take Off? A material take-off, also known as an “MTO” or “takeoff”, is a list of materials needed for the completion of a construction project. These materials may range from lumber and drywall to nails and screws. A material take-off can be used to create an accurate estimate of the cost of building a structure and helps contractors plan accordingly.
Creating a material takeoff can seem like an overwhelming task but it doesn’t have to be. With careful planning and organization, you can easily create an efficient MTO that meets all your needs while keeping costs down. To start, make sure you have accurate blueprints or plans of the job site as well as any necessary specifications for the materials being used in construction.
Step 1: Gather Necessary Documents
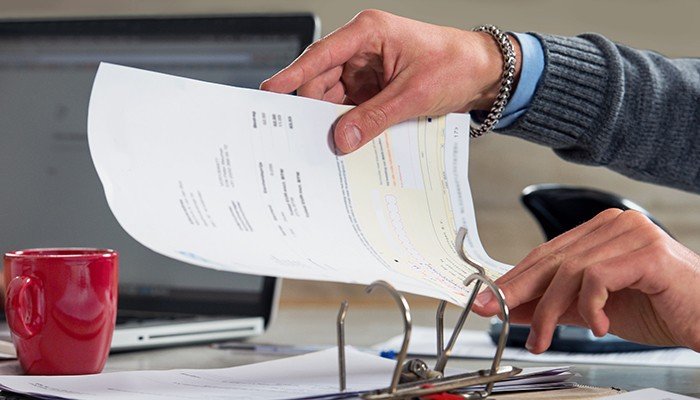
Creating a material take-off is an important part of any construction project. A material take-off is a list of all the materials needed for a specific task or job. It helps keep the project on track and allows for better budgeting. To create an effective material take-off, there are several steps you should follow:
The first step in creating a successful material take-off is to gather all necessary documents. This includes blueprints, drawings, and specifications. These documents provide essential information such as dimensions and quantities that will be needed to accurately estimate the cost of materials. Additionally, having accurate measurements from these documents will help avoid costly mistakes when ordering materials or building components.
Once you have all the necessary documents, it’s time to start itemizing the list of materials required for each component identified on your plans and specs sheet.
Step 2: Estimate Quantities and Measurements
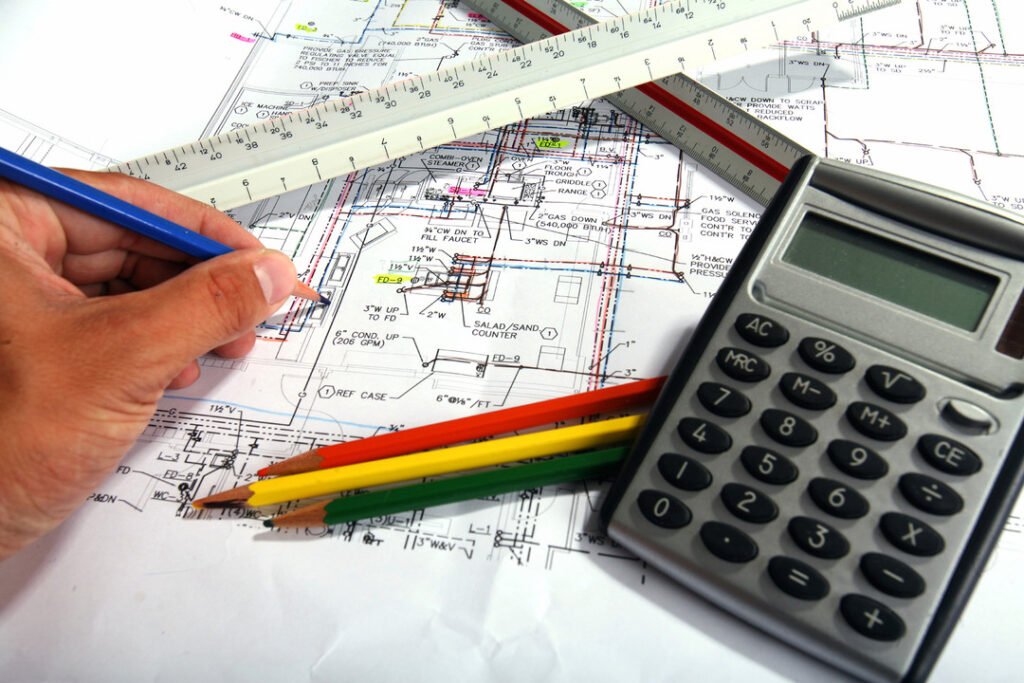
Creating a material take-off (MTO) is an important part of any construction project. An MTO helps estimate quantities and measurements needed for the job. In order to successfully create an MTO, it’s important to have a thorough understanding of the materials you will be working with.
The first step when creating an MTO is to compile all relevant drawings for the job. With these, you will need to identify all components that are necessary in order for your project to be completed. This includes any hardware or additional materials that may not be included in the original drawing such as screws, nails, and hangers. Once all components have been identified you can begin calculating each material’s quantity and measurements needed for use in your project.
Step 3: Calculate Costs and Account for Waste
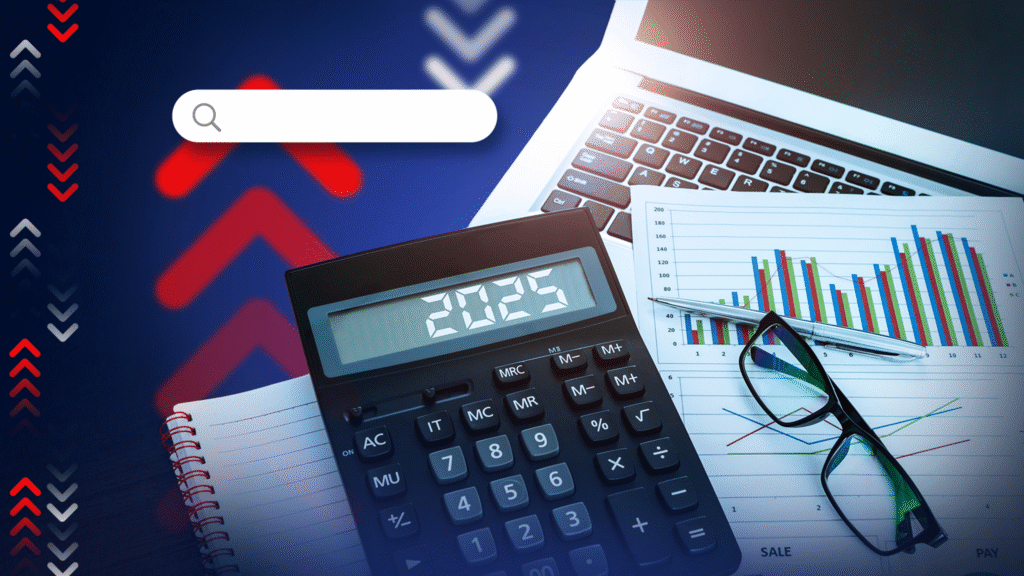
Creating a
The first step in creating an effective. It is to get organized – have all the necessary documents and drawings on hand. This includes both structural and architectural blueprints, as well as any material lists provided by suppliers or manufacturers. Once everything is gathered up, it’s time to break things down into individual items that need to be purchased or found on site. It’s also important to make sure that the measurements are accurate; otherwise, your calculations may be off when accounting for wastage and overages.
Step 4: Visualize and Revise
Creating a material take-off (MTO) is an important part of any construction project. An MTO is a list of materials, components, and equipment needed throughout a project and it helps keep track of necessary resources. Creating a detailed and accurate MTO can be tricky but with some planning and visualization tools, you can create one in no time!
Visualizing your project is the first step to creating an effective material take-off. Break down each task or phase into smaller elements that you can then assign to specific materials or components. During this process, it’s important to consider the full scope of the project, including any contingencies or changes that may come up during its completion. Make sure that everything you need for each stage is accounted for in your MTO so that it’s as accurate as possible when you get started!
Step 5: Finalize Listings and Reports
Creating a material take-off list is an important part of any construction project. It helps to ensure that all materials needed for the project are accounted for and that there are no surprises when it comes to budgeting and execution. Here’s how you can create one:
First, you want to gather all your drawings, plans, and specifications together. This way, you have everything in one place so you can quickly refer back to them when creating the material take-off list. Then, begin making an itemized list of each material needed for the project- from large equipment items down to tiny fasteners. Don’t forget any labor or installation costs if they will be needed as well! Once your list is complete, double-check it against your drawings and plans again before finalizing it.
Conclusion:
Creating a material take-off is a very important step in any construction project. Whether you are a contractor, owner, engineer or architect, it will benefit you to understand how to create and use this document. Using the above information as a guide should help you create an accurate and detailed material takeoff list. Afterward, make sure to review the list for accuracy and adjust if needed. With this knowledge, you can ensure that your project is completed with the right materials and at the right cost.